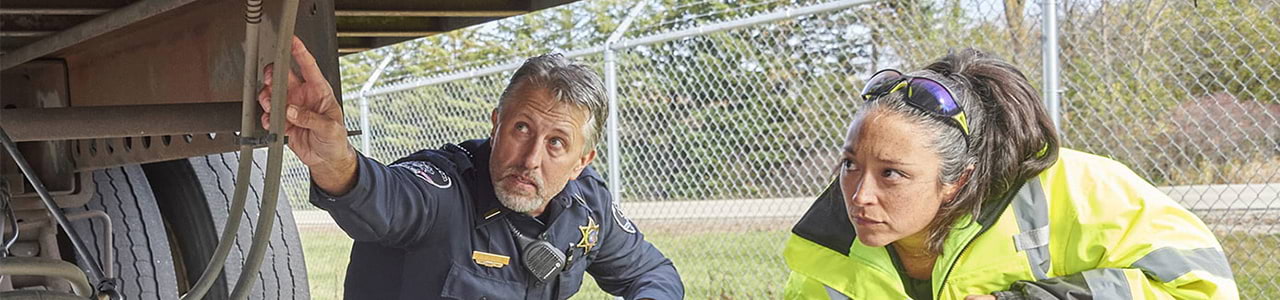
Roadside Inspections
Roadside inspections are the primary tool used by the FMCSA — the DOT administration that regulates commercial vehicles — to examine drivers, vehicles, and carriers to ensure they operate safely on the roadway. Roadside inspections help the FMCSA generate data on carriers and drivers to determine which ones are not operating compliantly and/or safely. They also provide industry-wide data on areas where carriers and drivers are having problems complying; and stop unsafe drivers, vehicles, and carriers.
According to the Commercial Vehicle Safety Alliance (CVSA), there are approximately 2.5 to 3.5 million inspections of commercial motor vehicles done each year in North America. Inspections are conducted by specially trained enforcement personnel and follow the procedures and criteria of the North American Inspection Program, created by the CVSA.
The results of roadside inspections can impact your Compliance, Safety, Accountability (CSA) score and your bottom line with costly repairs and fines. There are three possible outcomes of inspections:
- No violations are discovered;
- Violations are discovered, but the driver and vehicle are allowed to continue; or
- Violations are discovered, and they are serious enough the driver and/or vehicle are placed out of service.
A carrier’s goal is always that drivers receive no violations during roadside inspections as violations cause the FMCSA to look more closely at your company.
What You Need to Know
- A visible violation like a light not working, or entering an inspection facility with an obvious problem (overweight, loose cargo securement devices, etc.).
- A driving violation, such as speeding.
- A high ISS Score. The Inspection Selection System (ISS) score is a number between 0 and 100 and is based on the carrier’s safety performance in each of the seven Behavior Analysis and Safety Improvement Categories (BASICs). If the carrier’s score is above 50, it is likely to have more roadside inspections.
- Involvement in an accident. In most jurisdictions, a roadside inspection of any CMVs involved will be done following a serious accident.
- Random selection. Vehicles and drivers can also be randomly selected by an officer for inspection. However, there is truth to the statement that certain carriers, such as hazardous materials carriers and carriers with a poor safety or compliance record, are more prone to random inspections.
There are eight levels of inspections that can be conducted:
- Level I – North American Standard Inspection: a comprehensive, 37-step inspection of the driver and vehicle
- Level II – Walk-Around Driver/Vehicle Inspection: an inspection of driver and vehicle without physically getting under the vehicle
- Level III – Driver/Credential/Administrative Inspection: an inspection of the driver’s credentials and documents
- Level IV – Special Inspections: typically a one-time inspection of a specific item; normally conducted as part of a study or suspected trend analysis
- Level V – Vehicle-Only Inspection: the vehicle portion of a Level I inspection without a driver present; can be conducted at any location
- Level VI – North American Standard Inspection for Transuranic Waste and Highway Route Controlled Quantities (HRCQ) of Radioactive Material: an inspection of shipments containing transuranic waste and radioactive material, as defined by the Department of Transportation (DOT) and Department of Energy (DOE)
- Level VII – Jurisdictional Mandated Commercial Vehicle Inspection: a mandated inspection program that doesn’t fit the criteria of other levels; such as school buses, taxis, and limousines
- Level VIII – North American Standard Electronic Inspection: an electronically or wirelessly conducted inspection done while the vehicle is in motion without interaction with an inspector
The inspection will follow either a 13-, 34-, or 37-step procedure. The exact steps will depend on the level of inspection being conducted. The officer will begin the inspection by locating a suitable location for the inspection, making contact with the driver, and conducting a short interview. During the interview, the officer will be gathering information and assessing the driver’s condition. The officer will also collect and review the driver’s documents. If the officer is conducting a Level III (driver) inspection, the officer will document the findings and end the inspection at this point.
If the officer will also be conducting a vehicle inspection, the officer will provide the driver with detailed instructions. It is important that the driver pay attention and follow these instructions. The officer will then conduct a walkaround inspection of the vehicle, checking everything that is visible without going under the vehicle. If the officer is doing a Level I inspection, the officer will next go under the vehicle and inspect all of the underside components. The officer will also mark all of the brake pushrods, have the driver apply the brakes, and measure the brake freeplay.
Once done under the vehicle, the officer will check the tractor protection valve, the ABS, air leakage rate, steering lash, and fifth wheel freeplay. During this part of the inspection the officer will be in close contact with the driver and will be providing detailed instructions. Here again, it is very important that the driver pay close attention to the instructions and follow them to the letter.
The difference between a Level I and Level II inspection is when conducting a Level II inspection, the officer will not go under the vehicle.
Specific documents that must be provided to enforcement during inspections:
- Driver’s license
- Medical card (if applicable)
- Logs for current and previous seven consecutive days
- ELD user’s manual
- ELD malfunction instructions
- At least eight blank paper (or digital) logs
- Hours-of-service supporting documents
- Annual vehicle inspection report (or decal)
- Hazmat paperwork (if applicable)
- Vehicle registration or IFTA and IRP permit credentials (if applicable)
- Shipping papers (if applicable)
- Lease agreement (if applicable)
When a roadside inspection is completed, there are three possible outcomes:
- No violations were discovered,
- Violations were discovered, but the driver and vehicle are allowed to continue, or
- Violations were discovered, and they were serious enough the driver and/or vehicle are placed out of service.
The driver will be provided a copy of the inspection report. The driver needs to give the report to the motor carrier when arriving at the next terminal or facility. If the scheduled arrival is not with 24 hours, the report must be sent to the carrier. If a driver violation is recorded, the officer will determine if the violation meets the North American Out-of-Service Criteria. If it does, the driver will be placed out of service. Out-of-service driver violations must be corrected before the driver can operate any commercial vehicle.
If a vehicle passes a Level I, Level V, or Level VI inspection, the inspector will issue a CVSA decal. Generally, a vehicle with a CVSA decal will not be reinspected during the three-month period the sticker is valid.
If a vehicle has a violation, a CVSA decal will not be issued. If any of the vehicle violations meet the North American Out-of-Service Criteria, the vehicle will be placed out of service until all out-of-service violations are repaired.
Within 15 days the carrier must certify on the roadside inspection report that all violations have been corrected. A copy of the report must then be mailed or sent to the location provided on the report. The carrier must maintain a copy of the signed report for one year.
The 15-day requirements does not mean the carrier has 15 days to correct non-out-of-service violations. Driver violations must be corrected as soon as possible, and vehicle violations must be corrected the day of the inspection or included on a DVIR at the end of the day. When the vehicle violation is listed on a DVIR, it must be corrected before the vehicle can be operated again.
- Review Safety Measurement System data on a monthly basis to take proactive action on violations.
- Reduce your CSA BASIC scores by managing FMCSA compliance electronically.
- Share your roadside inspection data (including the most common violations you are receiving) with supervisors and drivers.
- Make sure you and all supervisors are familiar with the roadside inspection process.
- Improve vehicle maintenance practices to ensure vehicles are in the best possible condition when they are inspected.
- Train drivers on roadside inspections, including the process, what to expect and do, and the common violations discovered.
- Train drivers on the hours-of-service and record of duty status regulations (these two areas encompass the most common driver violations)
- Train drivers on conducting effective vehicle inspections.