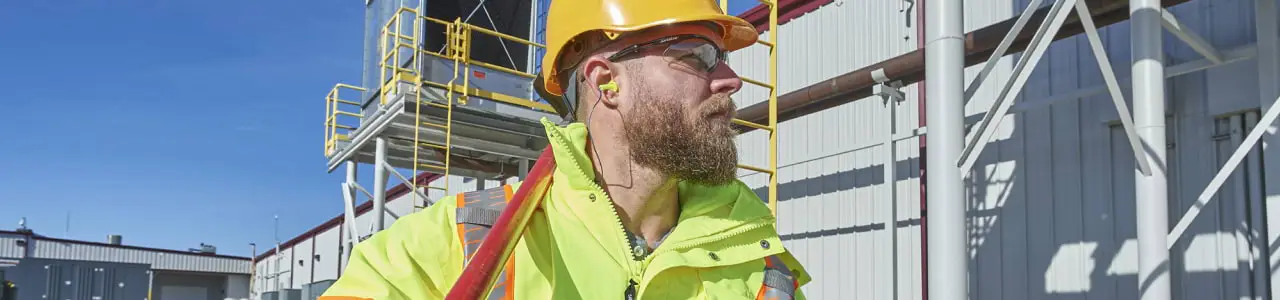
Construction, Utility & Energy
Construction workers comprise about 5 percent of the U.S. workforce but suffer 20 percent of work-related fatalities. Common hazards include falls (including those from cranes and derricks), excavation collapse, heavy equipment strikes, and electrocution. The construction industry also has high rates of non-fatal injuries. Hazards include working in temperature extremes and using equipment that requires eye, face, and hearing protection. Workers require training with regular reinforcement of safety rules to keep themselves safe. J. J. Keller offers the resources and services you need to protect workers from hazards in the construction, utility, and energy industries.Compliance Topics
Make sure you have the tools you need to comply with OSHA construction standards. See below for information and solutions on key construction safety topics.
Construction, Utility & Energy Services and Technology
The construction and utility industries are crucial for economic development. Similarly, employee and jobsite safety are crucial for the success of your operation and the health of your bottom line. Trust J. J. Keller’s experienced team of compliance experts to help you meet the wide range of compliance challenges you face.
- Chemical Management Service
- Environmental Audits & Assessments
- Environmental Compliance Programs
- Environmental Reporting Services
- Hazmat Compliance Programs
- OSHA Audits & Assessments
- OSHA Compliance Programs
- Hazmat & Multi-Modal Training
- Environmental Training
- OSHA Safety Training
- Safe & Smart® Forklift Operator Training & Trainer Certification
- Process Safety Management Services
- Human Resources Services
- Safety Management Suite
- Compliance Network
- Leave Manager
- J. J. Keller® Training
OSHA Construction and Jobsite Safety FAQs
With respect to forklift training, OSHA has adopted a performance-oriented approach to the qualifications of trainers and evaluators. The trainer and evaluator must be a person or persons with the requisite knowledge, training, and experience to conduct the required training and evaluations. An employer could assign a current employee, employ such instructors/evaluators, or contract with an outside service to conduct the required training and evaluation. Instructors/evaluators do not have to be a qualified or competent person as the terms are defined in the construction regulations.
No, it doesn’t meet OSHA requirements. Fire extinguishers must be immediately available to employees. When fire extinguishers are in a truck outside the building, employees can’t use them to eliminate a small fire and to help them escape. If employees can get to the truck, they are safe and there is no need to re-enter the burning building. In order to prevent theft, employees can take the fire extinguishers with them at the end of the shift and bring them back the next day. The extinguishers need only be on-site when the employees are actually working there.
If you remove the bucket from a front-end-loader and add forks, is the equipment then designated a forklift requiring the driver to be trained according to OSHA's new forklift training requirements? Or is the front-end-loader, wheel-loader, etc., still considered an earth mover? After a call to OSHA's Construction Division in Washington, D. C., the surprising answer is that OSHA still considers the equipment an earth mover. Why? Because, in their way of thinking, it is primarily a front-end-loader but is being used, probably on an infrequent basis, for forklift duties. Skid-steers with removable equipment and tool carriers also fit into this interpretation. Therefore, training is required but the requirements of 29 CFR §1910.178(l) do not have to be followed. However, the rule is a good guide for training on all heavy equipment.
When it comes to the OSHA rules, some companies must turn to both the 29 CFR §1910 Occupational Safety and Health Standards and 29 CFR §1926 Safety and Health Regulations for Construction for safety compliance requirements. A blanket statement such as, "We are a manufacturing company so we only follow the 1910 rules" just won't do. Ask yourself the question, "What is the activity my employees are involved in?" Some tasks are cut and dried. If your employee is running a drill press, or driving a forklift in a warehouse, it is general industry work and falls under the §1910 rules. If your employee is putting up siding at a construction site, you follow the §1926 rules.
Things start to change when, for example, a manufacturing company's management decides to physically expand their facilities and do the work themselves. When employees pick up hammers and saws to tear down an existing wall, they are now doing construction work and must be instructed in construction safety and health rules that apply to their work. Likewise, when a worker is working in a construction company's warehouse, doing general industry-type activities (such as stocking supplies using a forklift or doing metal fabrication work in a shop) employers and employees must follow the general industry rules. Once again, it's the activity that determines the rules you must follow, not the business type or physical setting.
In a letter of interpretation dated 12/16/1998, OSHA addressed the concerns of an employer regarding the use of electrical tape to repair minor damage (abrasions and cuts of limited depth) on the outer jacket of an extension cord. OSHA gives an in-depth answer to an age-old question for construction employers and employees.
Here is OSHA's response and the information you need when deciding to repair or replace that worn out or damaged extension cord:
You ask whether there is any prohibition against putting electrical tape over these kinds of abrasions and nicks when there is no damage beyond the jacket, the conductors have not been scraped or exposed, and the insulation inside the jacket has not been displaced or compressed. Generally, electrical tape may be used to cover superficial damage to cord jackets.
Section 1926.416(e)(1) [of the construction regulations] provides that "worn or frayed electrical cords or cables shall not be used." Superficial nicks or abrasions, those that only slightly penetrate the outer jacket of a flexible cord, and do not permit the cord to bend more in that area than in the rest of the cord, do not normally render a cord "worn or frayed." Therefore, there is no need to repair or replace such a cord.
Recommendation against taping
While taping these incidental abrasions and cuts does not necessarily violate any OSHA standard, we recommend that employers not tape this type of damage for two reasons. First, §1926.403(a) requires that "all electrical conductors and equipment shall be approved." This standard precludes the use of approved electrical conductors and equipment if their characteristics are significantly altered. Applying electrical tape that is too thick or applying too much of it could change the cord's original flexibility and lead to internal damage. Second, the depth of the abrasions and cuts cannot be monitored to see if they get worse without removing the tape.
It should also be kept in mind that the heavy duty extension cords commonly used on construction sites are designed to withstand a hostile environment. Damage to an extension cord that is bad enough to consider taping may have caused damage beyond the jacket.
Tape may not be used to repair significant damage to cord jackets
Repair or replacement of a flexible cord (depending on its gauge) is required when the outer jacket is deeply penetrated (enough to cause that part of the cord to bend more than the undamaged part) or penetrated completely, or when the conductors or their insulation inside are damaged.
Two provisions of the standard prohibit the repair of the jacket of a worn or frayed flexible cord with electrical tape. Section 1926.403(a) requires that the cord be approved. The original approval of the cord was based on the types of materials and construction used. As noted above, taping the cord can change the flexibility characteristics of the cord, which in turn can affect the amount of stress in the adjacent areas. This is of particular concern with respect to the grounding wire.
Also, the jacket is designed both to prevent damage to the conductors and insulators inside, and to further insulate the conductors. Taped repairs usually will not duplicate the cord's original characteristics. In most cases neither the jacket's strength nor flexibility characteristics will be restored. Therefore, tape repairs of the jacket may not be used to bring a worn or frayed flexible cord into compliance.
In addition, §1926.405(g)(2)(iii) states that "flexible cords shall be used only in continuous lengths without splice or tap. Hard service flexible cords No. 12 or larger may be repaired if spliced so that the splice retains the insulation, outer sheath properties, and usage characteristics of the cord being spliced." This standard precludes the repair of flexible cords smaller than No. 12.
Aerial lifts should be visually inspected prior to use and per manufacturer recommendations. OSHA provides a general checklist on which components should be tested and inspection. However, the manufacturer lists equipment specific checks listed in the operation manual. No documentation of the inspection is required, but it is a best practice to have a checklist that operators can use each time.
When a worker is working in an elevated position near overhead lines, the location shall be such that the person and the longest conductive object he or she may contact cannot come closer to any unguarded, energized overhead line than the following distances:
For voltages to ground 50 kV or below — 10 ft. (305 cm);
For voltages to ground over 50 kV — 10 ft. (305 cm) plus 4 in. (10 cm) for every 10 kV over 50 kV.
“Man lift” is a generic term used to reference various types of equipment used to lift a man. Most often, this term refers to aerial lifts (e.g., bucket trucks). If utilizing an aerial lift (as defined under 1910.67), OSHA views fall protection for these pieces of equipment differently than for scissor lifts.
The fall protection requirements for aerial lifts are outlined in 1910.67(c)(2). OSHA says that belting off to an adjacent pole, structure, or equipment when working from an aerial lift is not allowed. Workers have to be tied-off to the boom or the basket via a personal fall arrest or travel restraint system. Also, workers must always stand firmly on the floor of the basket, and can’t sit or climb on the edge of the basket or use planks, ladders, or other devices for a work position.
Yes. These employees need to use fall protection, unless the employer can demonstrate that is infeasible or would create a greater hazard that not using it. OSHA considered “climbing” to include going up and down the pole.
The standard requires that employees working from an aerial lift be protected by either a fall restraint system or a personal fall arrest system. A body belt connected to a lanyard cannot be used. A lanyard connected to a harness as part of a personal fall arrest system can be used, however.
OSHA references first aid by directing employers to the requirements under 1926.951. However, employers must provide more than first aid. OSHA says, “when employees are performing work on exposed lines or equipment at 50 volts or more, for field work involving two or more employees at a work location, at least two trained persons must be available.”
This means that employees must be trained in cardiopulmonary resuscitation (CPR). This is the same CPR training requirement for general industry employers as outlined under 1910.269(b)(1).
For fixed work locations like a substation, OSHA says the number of trained persons must be sufficient to ensure that each employee exposed to electric shock can be reached within 4 minutes by a trained person. However, where the existing number of employees is insufficient to meet this requirement (at a remote substation, for example), each employee at the work location has to be a trained employee.
The two-person rule is addressed at 1926.960. Except as provided in paragraph (b)(3)(ii), at least two employees must be present while any employee performs the following types of work:
- Installation, removal, or repair of lines energized at more than 600 volts,
- Installation, removal, or repair of de-energized lines if an employee is exposed to contact with other parts energized at more than 600 volts,
- Installation, removal, or repair of equipment, such as transformers, capacitors, and regulators, if an employee is exposed to contact with parts energized at more than 600 volts,
- Work involving the use of mechanical equipment, other than insulated aerial lifts, near parts energized at more than 600 volts, and
- Other work that exposes an employee to electrical hazards greater than, or equal to, the electrical hazards posed by operations listed specifically in paragraphs (b)(3)(i)(A) through (b)(3)(i)(D).
The reason for the two-person rule is that the second person can begin to administer CPR within four minutes after an employee loses consciousness due to an electric shock.