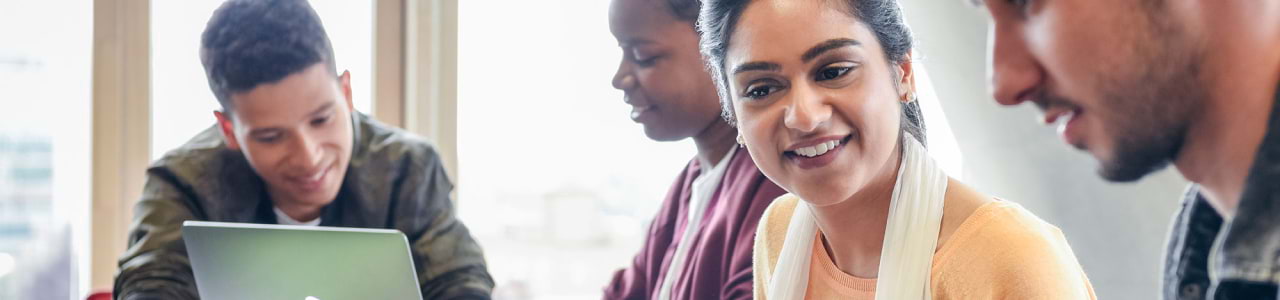
Education
Education employees may be at risk from bloodborne pathogens, infectious diseases, cleaning chemicals, and slips or falls. These employers must also follow environmental regulations, such as managing waste fluorescent tubes. Although federal OSHA does not cover public education, half the states operate plans that apply equivalent standards to public employers, and the remaining states usually adopt similar standards. Private schools are covered by OSHA, and both public and private schools have environmental obligations. J. J. Keller’s OSHA training resources and expert support can help your workers protect themselves and comply with OSHA and environmental regulations.Compliance Topics
Make sure you have the resources you need to comply with education-related standards. See below for information and solutions on key topics.
Frequently Asked Questions
Education
While OSHA highly recommends that facilities have AEDs, OSHA does not require them. However, some states require that certain facilities have AEDs. These facilities could include:
- Schools (public and private)
- State buildings
- Sports venues
- Gambling parlors
- Non-health facilities
That’s why your state and local codes should be reviewed on a regulator basis to keep current with the requirements.
Unfortunately, OSHA doesn't break out higher education establishments from the rest of "general industry." So, covered universities would be covered by the same standards as those for manufacturers, retailers, etc. The OSHA standards are hazard-based or equipment/process-based, rather than industry-based, for the most part.
For example, if you have a laboratory, then that could trigger some requirements, if you have certain specific chemicals, those could trigger requirements, if you operate forklifts or powered pallet jacks, workers would need training, if workers work at heights or are exposed to fall hazards, training would be needed. Other issues that might be common to your type of settings include: electrical, aerial lifts, sanitation, asbestos if doing renovation on buildings, emergency action plans, and fire safety.
At the Federal OSHA level, no. The term “employer” as it relates to OSHA is a person engaged in a business affecting commerce who has employees but does not include … any State or political subdivision of a State. Government entities do not meet the definition of an employer under the OSH Act. This means that they not subject to OSHA’s federal regulation, inspection, or enforcement.
OSHA state plans vary from state to state, some keep the Federal employer definition and do not include school systems. However, many states do cover public schools, depending on how employer is defined in the state statutes. Private schools are considered employers under the act and are subject to Federal OSHA jurisdiction, as are some charter schools, depending on their administrative structure and governance.
At 1910.36(g)(2) OSHA states that “an exit access must be at least 28 inches (71.1 cm) wide at all points.” [bold emphasis added] OSHA defines an exit access as “that portion of an exit route that leads to an exit.” This would include aisles, doorways, hallways, ramps, passageways, etc. that may be used to get to an exit.
OSHA further addresses this issue in several Letters of Interpretation (LOI). In the first, dated April 27, 2000, an employer asks whether or not the minimum width of any way of exit access must be at least 28 inches in width. OSHA response is ‘yes’. Also, in a November 15, 1993 LOI in which a company asks whether the width of a doorway that is 27 5/8 inches wide is in compliance with the above requirement, OSHA’s response is that “...the deficit of 3/8 inch (0.9 cm) in width would be considered a de minimis violation having no adverse impact on the safety and health of employees.”
OSHA defines an exit route as “a continuous and unobstructed path of exit travel from any point within a workplace to a place of safety.”
OSHA requires at 1910.37(b)(6) that each exit sign “be illuminated to a surface value of at least five foot-candles by a reliable light source.” In addition, self-luminous or electroluminescent signs that have a minimum luminance surface value of at least .06 footlamberts (0.21 cd/m2) are permitted. In other words, exit signs don’t necessarily need to be illuminated with a bulb, but must be illuminated to the five foot candle requirement.
OSHA requires at 1910.37(b)(6) that each exit sign “be illuminated to a surface value of at least five foot-candles by a reliable light source.” If emergency lighting provides the necessary illumination, then that is all that is needed. However, if emergency lighting were to fail, and the exit signs were not properly illuminated, then the employer would be in violation of the standard.
No. OSHA requires under 1910.36(d) that “employees must be able to open an exit route door from the inside at all times without keys, tools, or special knowledge.” [bold emphasis added] OSHA further emphasizes this requirement in a December 19, 1991 Letter of Interpretation that clearly states exit doors must not be locked or obstructed in any way or at any time.
Door(s) that “connect any room to an exit route must swing out in the direction of exit travel if the room is designed to be occupied by more than 50 people or if the room is a high hazard area...” at 1910.36(e)(2).
OSHA does not require exit doors to be numbered; however, numbering doors is an effective means of directing people or services (e.g., fire and police departments) to a particular location at a facility.
OSHA’s position is that EPA-registered tuberculocidal disinfectants, diluted bleach solutions, and EPA-registered disinfectants that are labeled as effective against both HIV and HBV as well as sterilants/high-level disinfectants cleared by the FDA, meet the requirement in the standard and are “appropriate” disinfectants to clean contaminated surfaces, provided that such surfaces do not become contaminated with agent(s) or volumes of or concentrations of agent(s) for which higher level disinfection is recommended. The particular disinfectant used, as well as the frequency with which it is used, will depend upon the circumstances in which a given housekeeping task occurs (i.e., location within the facility, type of surface to be cleaned, type of soil present, and tasks and procedures being performed). The employer’s written schedule for cleaning and decontamination should identify such specifics on a task-by-task basis.