Safety Data Sheet Search
Quickly find the Safety Data Sheets you need!
Simply enter your search term below and click “Search.” It’s that easy!.
Safety Data Sheets FAQs
SDS stands for Safety Data Sheet, formerly known as a Material Safety Data Sheet, or MSDS
Employers must have a GHS-style, 16-section SDS for each chemical which is considered to be a health or physical hazard as those terms are defined in the standard, except for those products specifically exempted under the hazcom regulation at 1910.1200(b)(6).
OSHA defines "health hazard" as "a chemical which is classified as posing one of the following hazardous effects: acute toxicity (any route of exposure); skin corrosion or irritation; serious eye damage or eye irritation; respiratory or skin sensitization; germ cell mutagenicity; carcinogenicity; reproductive toxicity; specific target organ toxicity (single or repeated exposure); or aspiration hazard."
OSHA defines a "physical hazard" as "a chemical that is classified as posing one of the following hazardous effects: explosive; flammable (gases, aerosols, liquids, or solids); oxidizer (liquid, solid or gas); self-reactive; pyrophoric (liquid or solid); self-heating; organic peroxide; corrosive to metal; gas under pressure; or in contact with water emits flammable gas."
You are not required to have SDSs for household consumer products when the products are used in the workplace in the same manner that a consumer would use them, i.e., where the duration and frequency of use (and therefore exposure) is not greater than what the typical consumer would experience.
This exemption is based, however, not upon the chemical manufacturer's intended use of the product, but upon how it is used in the workplace. Employees who are required to work with hazardous chemicals in a manner that result in a duration and frequency of exposure greater than what a normal consumer would experience need to be trained on the hazards of that product.
Non-hazardous chemicals are not covered by HazCom; therefore, SDSs are not required for those chemicals. Since OSHA does not require nor encourage employers to maintain SDSs for non-hazardous chemicals, an employer is free to discard SDSs for non-hazardous chemicals.
SDSs must be in the language of the employees that work at your workplace. You are required to have them in English, but if most of your employees speak Spanish, then you must have the SDS in Spanish as well. The standard states it must be in the language that an employee can understand. If you have employees that speak other languages, then you must accommodate those employees with the SDSs in their language as well.
OSHA says in 1910.1200(g)(8) that it is permissible to provide access to SDSs from an electronic work station in the employee's work area provided the employee knows how to access the SDSs. OSHA further says in 19190.1200(g)(9) that where employees must travel between workplaces during a work shift, i.e., their work is carried out at more than one geographical location, the safety data sheets may be kept at the primary workplace facility. In this situation, the employer shall ensure that employees can immediately obtain the required information in an emergency. However, the SDSs can’t be locked up at any point in time by the employer.
Other Hazard Communication Solutions
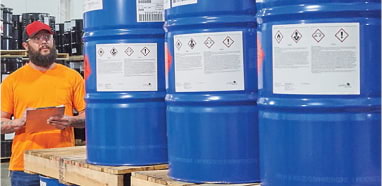
J. J. Keller® Safety Management Suite
J. J. Keller® Safety Management Suite has the tools needed to develop, implement and maintain a compliant workplace safety program with access to SDSs and GHS-compliant labels.
Learn More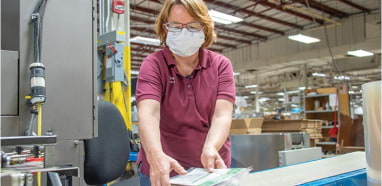
OSHA Compliance Program
J. J. Keller consultants assess your OSHA compliance and safety risks and provide ongoing guidance and resources to improve workplace safety. An on-site assessment can focus on your hazard communication program and SDS review and analysis.
Learn More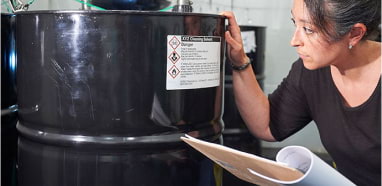
Chemical Management Service
Work with J. J. Keller consultants and have your HazCom program managed for you. Our full-service chemical management service is tailored to your needs and includes a HazCom program assessment, chemical inventory creation, SDS and label management, training, and program reporting.
Learn More